V-Seals
V-seals are crucial in keeping dirt, moisture, and other harmful contaminants away from essential machinery components while effectively retaining lubricants. Their adaptable design helps improve the efficiency and lifespan of mechanical systems. These seals stretch over the shaft, forming a secure fit, while their flexible lip lightly contacts the counterface at a right angle, establishing a strong defense against external elements. Although V-seals function efficiently on their own, they provide optimal protection when paired with rotary shaft seals. This combination helps extend the service life of bearings, oil seals, and shafts by reinforcing contamination prevention and maintaining lubrication.
Colonial Seal Company supplies V-seals in multiple configurations and materials, including Viton, NBR, silicone, and EPDM.
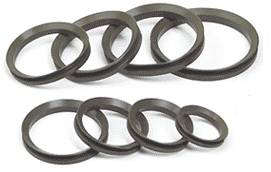
Advantages of V-Seals
V-seals offer numerous benefits, making them a reliable sealing solution across a variety of industries.
Highly adaptable and can fit a broad range of shaft sizes, making them suitable for diverse industrial applications.
By keeping contaminants out and retaining lubricants, V-seals help prolong the lifespan of bearings, shafts, and oil seals, minimizing maintenance costs and downtime.
Their flexible lip design allows them to accommodate shaft movements and surface variations, ensuring a secure and consistent seal under different operating conditions.
Easy to install and remove, these seals do not require special tools.
Manufactured from durable materials, V-seals withstand extreme temperatures, exposure to chemicals, and abrasive environments.
Their low-friction design enhances machine efficiency while reducing energy consumption.
Types of V-Seals Available
Colonial Seal Company provides V-seals in different styles to meet specific application needs. We offer three primary designs—VA, VS, and VL—available in two material options: NBR (black) and Viton® (brown).
VA Style: One of the most commonly used V-seals, featuring a straight back face, standard cross-section, and a short mounting length. Available in sizes ranging from 2.5mm ID to 1,810mm ID, they are ideal for protecting bearings in gearboxes, electric motors, and drive systems.
VS Style: Recognized for its wide body, low cross-section, and tapered back face, this type provides a secure grip on the shaft and is frequently used in agricultural and automotive applications. Offered in sizes from 4mm ID to 180mm ID.
VL Style: Designed for compact applications, this type has a reduced axial cross-section and short mounting length, making it a great replacement for labyrinth seals. Available in sizes ranging from 99mm ID to 540mm ID.
Applications of V-Seals
V-seals are widely used in various industries, offering effective sealing solutions for:
Electric Motors: Protects motors from contaminants, helping maintain efficiency and prevent premature wear.
Gearboxes: Prevents dirt and moisture from entering, ensuring smooth operation and extending the life of gears and lubricants.
Automotive Components: Used in axles, drive shafts, and gearboxes to keep contaminants out and maintain optimal performance.
Mining Equipment: Shields machinery from harsh conditions and abrasive particles found in mining environments.
Pumps: Prevents the entry of dirt and moisture, ensuring consistent performance and reducing maintenance requirements.
Drive Systems: Helps retain lubrication while keeping contaminants at bay, ensuring the longevity of key components.
Selecting the Right V-Seal
When choosing the appropriate V-seal for your application, consider the following factors:
Size: Ensure the seal matches your shaft diameter. Our size charts and experts can help determine the right fit.
Material: Choose the material based on operating conditions. NBR (black) offers good oil and grease resistance for general applications, while Viton® (brown) is suitable for high temperatures and exposure to aggressive chemicals.
Operating Conditions: Assess factors such as temperature range, chemical exposure, and environmental conditions to ensure the seal’s material and design meet your needs.
Compatibility: If using the V-seal with other seals, such as rotary shaft seals, verify compatibility to enhance sealing performance.
Mounting Length: Consider available space—VA and VL styles are ideal for applications with limited mounting room.
Performance Needs: Evaluate durability, friction levels, and wear resistance to ensure the seal meets operational demands.
Installing V-Seals
Installing a V-seal is a straightforward process:
Prepare the Shaft: Clean the shaft to remove dirt, moisture, and debris. Inspect for damage or sharp edges that may harm the seal during installation.
Check Compatibility: Ensure you have the correct size and style of seal for your application.
Fit the Seal: Carefully stretch the V-seal over the shaft without excessive force or using sharp tools that could damage it.
Position Correctly: Place the seal so that its flexible lip faces the counterface at a right angle to the shaft, ensuring proper alignment.
Secure in Place: Adjust the seal to sit evenly and snugly on the shaft, verifying that the sealing lip maintains uniform contact with the counterface.
Test Rotation: Manually rotate the shaft to ensure the V-seal moves smoothly while maintaining contact with the counterface.
At Colonial Seal Company, we provide expert guidance to help you find the ideal sealing solution for your application. We offer replacements for leading brands such as SKF, Chicago Rawhide, Trelleborg, and Freudenberg. Our deep expertise in materials and industrial sealing applications allows us to deliver durable, high-performance V-seals tailored to your needs.