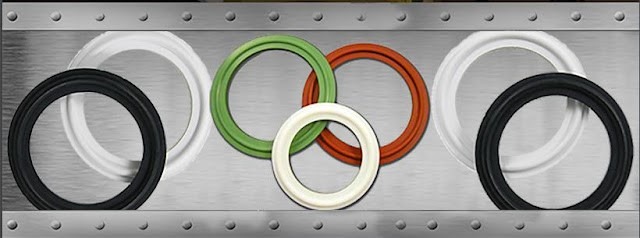
Frequently asked to provide gaskets complying with Food and Drug Administration (FDA) regulations, gasket manufacturers are often left to face this broad and complex area that often extends far beyond consumable, digested products. This information will help explain many of the requirements for FDA compliant gaskets and why they exist. What does it mean to conform to FDA regulations? Gaskets are considered FDA approved through GRAS, existing FDA regulations, and FDA FCN.
GRAS – Materials that are generally regarded as safe (GRAS). Many materials that have been used successfully in FDA applications are listed as GRAS. Through scientific procedures, the use of a food substance gasket may be GRAS for a substance used in food before 1958 or through experience based on common use in food. However, some materials are already covered by existing regulations. For example, perfluorocarbon resins and PTFE are found in 21 CFR 177.1550. These would fall under the category “existing FDA regulations.” New materials that are not covered by either of these previous choices can be submitted to the FDA through a food control notification (FCN).
The most common gasket materials used for FDA applications are PTFE gaskets. Covered in 21 CFR 177.1550, filled gaskets made entirely from PTFE may be used if the filler/s, coloring agents, etc., are considered GRAS or if they are covered by another regulation. Extractable tests with maximum limitations are also required based on the surface area of the sample. Some gasket materials, such as PTFE joint sealant, are supplied with an adhesive strip to make installation easier. The adhesives must conform to 21 CFR 175.105.
Non-PTFE used materials include elastomer (rubber that is able to conform to FDA regulations and is used in many flat-faced flanges in which the available compressive load is low.) Finding an elastomer suited for the media contained in the given particular system is made possible since compounds can be created from most elastomer types (NBR, SBR and EPDM.)
21 CFR 177.2600 lists acceptable elastomers, as well as acceptable fillers, processing agents, additives and curative systems. Gaskets made from elastomers are covered under this section. Acceptable levels for each component are listed, extraction tests and limitations are identified, and the test fluids are based on the intended specificity of service. An example of this could be that different extractions tests are done for fatty- versus aqueous-based food service.
Some gasket products may also include an adhesive used as an assembly aid. While there is no real “sealing function” performed by such adhesives, since they are used primarily to secure the gasket into position prior to assembly, these adhesives must also meet certain requirements mandated by the FDA. An example of an adhesive used with PTFE material might be an acrylic that is composed of 2-ethylhexyl acrylate, butyl acrylate, methyl methacrylate and glycerin rosin ether. All four compounds are included in 21 CFR 175.105 as acceptable substances.
Proper identification of a gasket material may be necessary in order to provide traceability for the end-user. This requirement is usually satisfied by printing the manufacturer’s name or brand name and style number on one or both sides of the gasket sheet. Once converted to the specified gasket configuration, the ink may also come into contact with the process media (therefor it must also meet certain CFR criteria.) All branding ink ingredients must be acceptable for direct contact with food and pharmaceutical products in accordance with appropriate sections of 21CFR.
Various FDA applications use piping with sanitary couplings (such as breweries, wineries, and dairy product plants.) These couplings are made to be easily disassembled so that the system can be cleaned. These specialized seals or gaskets used in these couplings are normally made in a specific shape and cross-section to easily conform under the low available compressive load. These seals are made from many materials including PTFE, elastomers (with or without metal inserts), etc.
For applications that involve food and pharmaceuticals, other requirements may be needed for compliance beyond those of the FDA. These include those of National Sanitary Foundation (NSF), U.S. Pharmacopeias (USP) and 3A. For instance, a certification to meet the U.S. Pharmacopeia Plastic Class VI Requirement is a frequent request. This biological reactivity test requires samples of the gasket material to be tested by implanting them into live animals to confirm that no toxic reactions occur from the material. (Tests must be completed by approved laboratories recognized by the U.S. Pharmacopeia.)
Many countries have changed many of the regulations specific to direct and indirect contact with food, pharmaceutical, and related products. Examples of this are the recent changes in the Official Journal of the European Union Regulation (EC) No 1935/2004. This regulation lays out the principals for any material or article that comes into contact with food. This regulation along with (EC) 2023/2006/EC lays out the principals of good manufacturing practice (GMP) and demonstrates similar practices and concerns as those here in the U.S.
The above information is provided only as a guide in helping you understand how gaskets may comply with the Food and Drug Administration. Please call Colonial Seal Company at 856-432-0012 or email sales@colonialseal.com for more information.
Founded in 1994, Colonial Seal Co. is headquartered in Westville, New Jersey. Colonial Seal specializes in oil & grease seals, hydraulic seals, rotary shaft seals, mechanical seals, rubber molded products and gaskets. Through a global network of manufacturers, Colonial Seal can produce custom seals designed for a client’s unique sealing applications. Colonial Seal Company is ISO 9001:2008 certified.